- News and Events
- News
- 2023.06, A One-Stop Emission Solution Provider
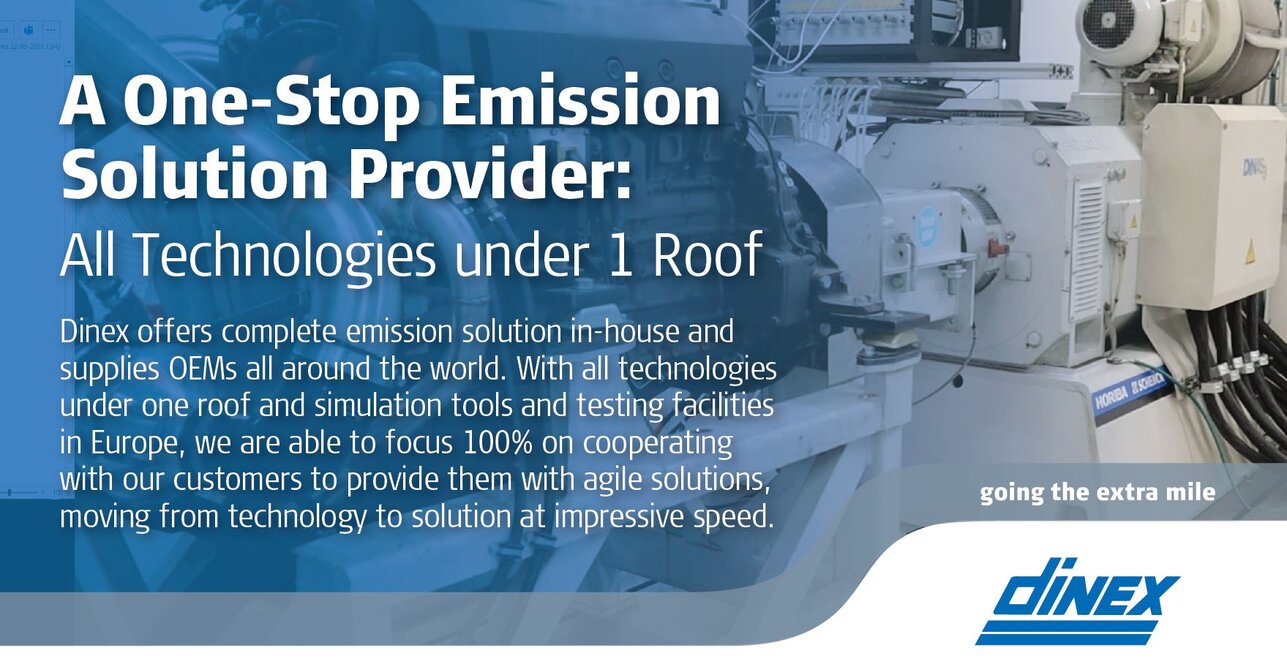
All Technologies under 1 Roof
Dinex is the only supplier in the Heavy-Duty industry that holds competences for both development and production of all components of a complete emission solution in-house (Turbo to Tailpipe). Everything from design & simulations, upand downstream piping, thermal insulation and
decoupling elements, to ceramic HP-SiC & metallic substrates, catalytic coatings, and canning, is all based on Dinex’ own innovative technologies. And that includes also the competences required to put all the “bricks” together, to design, simulate, and finally test and validate the solution.
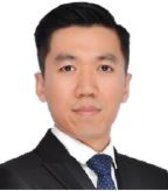
Jerry Song
Head of Commercial and Engineering, Dinex China
“Dinex believes that a deep, holistic technology insight and quick response are two keys to succeed in diverse local markets all over the world, such as the Chinese. Our organization has spent a lot of effort in past years to localize technologies and processes to China, supported by global Dinex competences. We will keep offering customers value-added solutions thanks to quick decision making and complete in-house ownership of all core technologies.”
In-house Testing Facilities in Europe, with Global Mindset
Dinex has in-house testing facilities where we are fully equipped to test samples and provide feedback on performance, and in addition we have close collaboration with local partners globally. Our centralized testing facilities are in Europe and serve customers from all regions of the world daily. By maintaining our core technical competences within the same location, we guarantee our customers the same high level of service, supported by decades of first-hand experience from similar markets and applications. As secondary solution, our local partners can support with urgent local tasks where it is deemed unfeasible to test in Europe, with online support from our global competences to give our customers the same benefits.
We have a proven track-record for supporting our local development teams with global competences. In recent years we started cooperation with Ashok Leyland, to establish Dinex India from nothing to a PPAP-approved BS-VI solution, new local production site, and an on-boarded local organization in just 1 year.
Whilst building the factory in India, the test centers in Europe were supporting Dinex project management and Ashok Leyland in testing their H4 truck platform, ensuring that all tests were completed and the BS-VI solution was ready to be set in production by the scheduled SOP in 2021, thus proving Dinex’s testing capabilities to serve customers globally.
Simulations is the Fast-Track
Dinex uses simulation as a valuable tool for the design of aftertreatment system canning components and catalytic performance. Our simulations are built on a broad package that covers Computational Flow Dynamics (CFD) simulations to evaluate flow uniformity and pressure drop, to transmission loss, harmonics, and other levels of chemical as well as mechanical design like Finite Element Analysis (FEA).
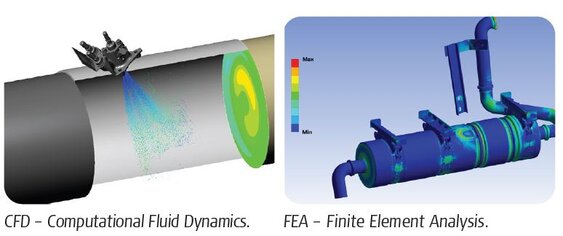
At our headquarter offices in Denmark an entire team of skilled professionals has over 20 years of experience in applying the full simulation toolbox to create better solutions for our customers, in a faster, more agile and efficient development process with less backflows.
Our simulation software has a comprehensive library of generic reactions for all existing catalyst technologies within Dinex, allowing for fine tuning into accurate reaction models that help the product development and application teams to deliver solutions to our customers problems, even before practical experiments take place, limiting the number of samples for testing whilst keeping the performance of samples which make it through to testing significantly higher than the alternative.
Dinex and KOHLER’s mutual journey to Stage V
In 2017 Dinex and KOHLER commenced on a journey to meet the Stage V legislation limits. The result of this collaboration was a modular, scalable, and serviceable system, able to adapt to different vehicle layouts and configurations, a flexibility requirement of the utmost importance in off road applications.
With a development cycle of 3 years, the concept development included CFD simulations to assess design, flow, pressure drop and thermal management aspects. Extensive testing was conducted at Dinex’ laboratories ranging from SGB to engine bench testing to evaluate emission performance and endurance of the DOC-DPF concepts. Thorough FEA testing was also conducted to ensure all mechanical durability aspects surrounding the very different designs and components involved were accounted for.
In Dinex, finding solutions for customers is always the priority. Thanks to remarkable teamwork and commitment to high quality engineering with closely involved teams around the world, Dinex provides an effortless service that is both agile and global.
To learn more about Dinex emission control solutions, you are most welcome to contact our CSO, Mr Lennart Rasmussen, our CTO, Mr Evangelos Georgiadis, and our Head of Commercial and Engineering in China, Mr Jerry Song.
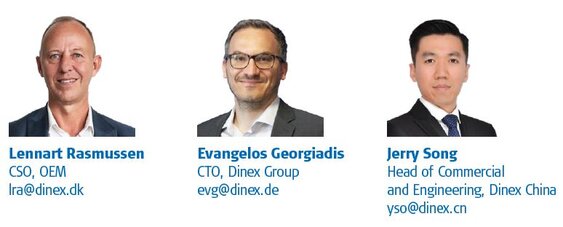
A glimpse of the Dinex OEM Division
Global Footprint - Local Presence
Operating with local teams close to our customers, backed up by global technical competences.
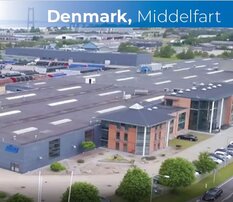
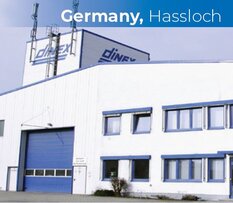
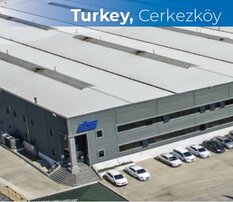

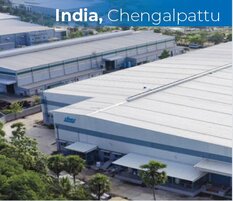
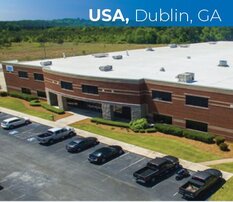
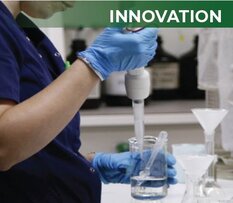
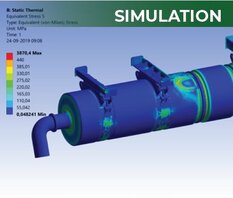
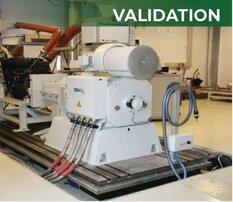
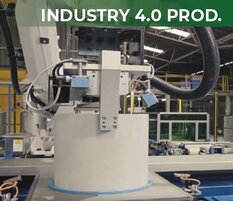
Core Technologies - Proven Solutions
All developed and produced in-house for a simple, cost efficient supply chain with highest solution ownership.
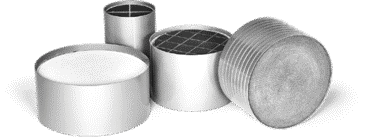
Ceramic and Metallic
Substrates with catalytic coating
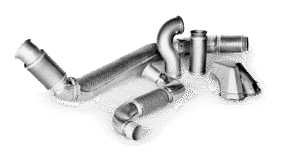
Pipes, Zero-Leakage Decoupling
and Thermal Management
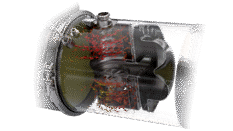
Canning and system integration
with optimal flow and mixing
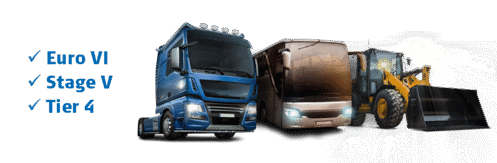
Agile Partnership - Customized Innovations
Full System and customer specific engineering approach: From final application down to coating formula.
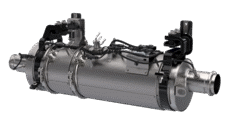
In-line system
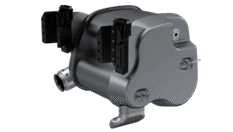
Box system
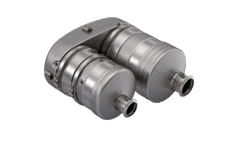
U-Shape system
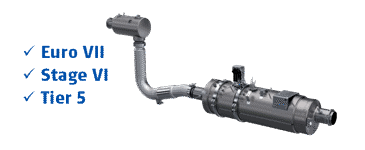
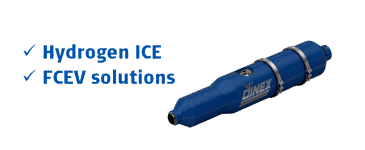